Understanding Rapid Prototype Manufacturing
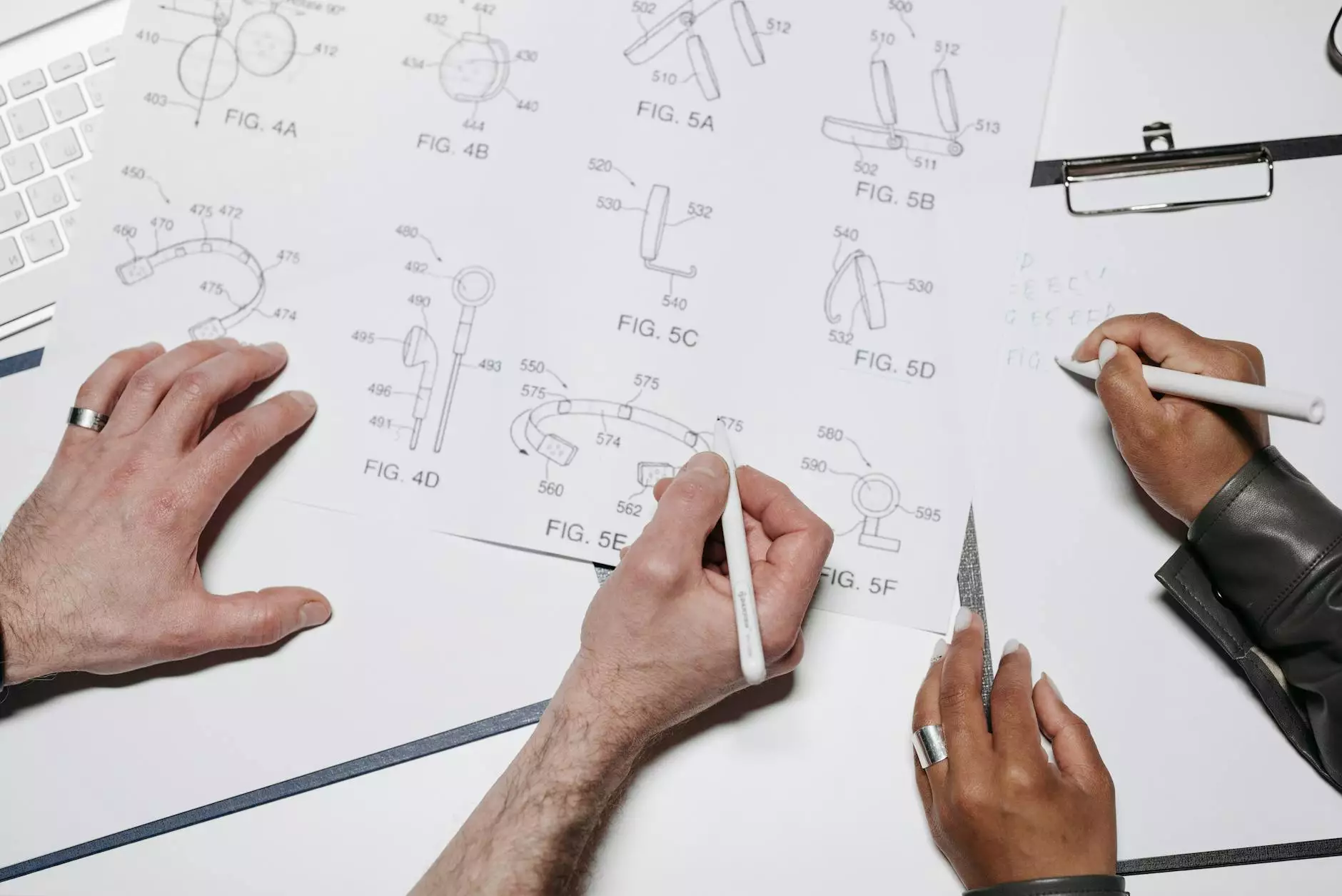
Rapid prototype manufacturing is revolutionizing the way businesses approach design and production. This innovative technology enables companies to create a tangible model of their product ideas rapidly, which is an essential step in the development cycle. In the competitive realm of metal fabrication, businesses like DeepMould are increasingly utilizing rapid prototyping to enhance their offerings and improve customer satisfaction.
What is Rapid Prototype Manufacturing?
At its core, rapid prototype manufacturing is the process of quickly fabricating a scale model of a physical part or assembly using three-dimensional computer-aided design (CAD) data. It employs various techniques and materials to create these models, which can range from plastics to metals.
The Processes Involved
There are several well-known methods within rapid prototyping, each with its own advantages and use cases. Here’s a brief overview:
- Stereolithography (SLA): A technique that uses a laser to cure liquid resin into hard plastic, known for its high accuracy and detail.
- Selective Laser Sintering (SLS): A method that utilizes a laser to fuse powder materials, creating durable prototypes ideal for functional testing.
- Fused Deposition Modeling (FDM): A popular additive manufacturing technology that feeds thermoplastic filaments through a heated nozzle to build parts layer by layer.
- Direct Metal Laser Sintering (DMLS): Specializing in metal parts, this technique uses lasers to sinter powdered metal materials, resulting in strong, complex geometries.
Advantages of Rapid Prototype Manufacturing
Utilizing rapid prototype manufacturing offers a multitude of benefits, especially for businesses in the metal fabrication sector. Here are some key advantages:
1. Speed to Market
The ability to quickly create prototypes significantly accelerates the product development timeline. Companies can produce and test models within days, allowing them to respond rapidly to market demands.
2. Cost Efficiency
While traditional manufacturing can be expensive and time-consuming, rapid prototyping minimizes costs associated with design errors and excessive production runs. Companies can accurately gauge the feasibility of their designs before committing to full-scale production.
3. Enhanced Design Precision
Advanced technologies used in rapid prototype manufacturing ensure that prototypes are created with a high degree of precision. This reduces the likelihood of costly revisions during the final manufacturing phases.
4. Innovation Catalyst
With rapid feedback from actual prototypes, teams can explore more creative solutions and refine their ideas efficiently. This iterative process fosters innovation, allowing companies to stay ahead of the competition.
Case Studies: Transformative Implementations
Several businesses have successfully integrated rapid prototype manufacturing into their operations, yielding incredible results. Below are a few notable examples:
DeepMould: Pioneering Metal Fabrication
DeepMould, a leader in the metal fabrication industry, has adopted rapid prototyping into its design and production processes. By utilizing techniques like DMLS, they can produce complex metal parts that were previously impossible to manufacture. This shift not only improves their speed but also enhances the quality of their products.
Aerospace Industry
The aerospace sector employs rapid prototyping to create lightweight yet strong components. Companies have reported reduced lead times and enhanced performance as a result of using DMLS for critical parts.
Automotive Innovations
In the automotive industry, firms are turning to rapid prototyping to test new designs and variations with the goal of improving efficiency and performance. The flexibility and speed of this manufacturing approach have redefined how prototyping is perceived within the industry.
Challenges Encountered in Rapid Prototyping
Although rapid prototype manufacturing presents numerous advantages, it is not without its challenges. Addressing these challenges is crucial for successful implementation:
1. Material Limitations
Choosing the right materials for rapid prototypes can be difficult. Not all materials used in rapid prototyping reflect the properties of the final product, which can lead to discrepancies in testing and outcomes.
2. Technology Costs
While costs associated with traditional manufacturing processes can be high, the upfront investment in rapid prototyping equipment and technology can also be significant. However, the long-term savings often justify these initial expenses.
3. Skill Requirements
Adopting advanced technologies necessitates skilled personnel who understand both the software for CAD and the equipment used for prototyping. Investing in training is essential for capitalizing on the benefits of rapid prototyping.
Future Trends in Rapid Prototype Manufacturing
The future of rapid prototype manufacturing looks promising. Here are some trends shaping the future of this field:
1. Increased Use of AI and Machine Learning
As artificial intelligence and machine learning technology advance, they are increasingly being integrated into manufacturing processes. Companies expect to see improved efficiencies and predictive analytics, leading to less downtime and reduced costs.
2. Sustainable Practices
With growing concerns about environmental impact, the industry is leaning towards more sustainable materials and processes. Rapid prototyping can facilitate the adoption of eco-friendly practices, from reducing waste to utilizing recyclable materials.
3. Integration with IoT
The Internet of Things (IoT) offers new possibilities for connectivity and data sharing within manufacturing environments. Companies can achieve real-time data collection and analysis, enhancing decision-making processes related to prototyping.
Conclusion
In conclusion, rapid prototype manufacturing is transforming the landscape of metal fabrication. Companies like DeepMould are harnessing its power to improve efficiency, reduce costs, and drive innovation. As we move into the future, the continuous evolution of this technology will undoubtedly lead to even greater advancements in the industry.
Call to Action
For businesses interested in staying competitive in the ever-evolving market, embracing rapid prototyping is essential. Explore how leveraging rapid prototype manufacturing can enhance your design processes and improve your product offerings today!