Understanding Plastic Injection Mould Manufacturing: A Detailed Guide
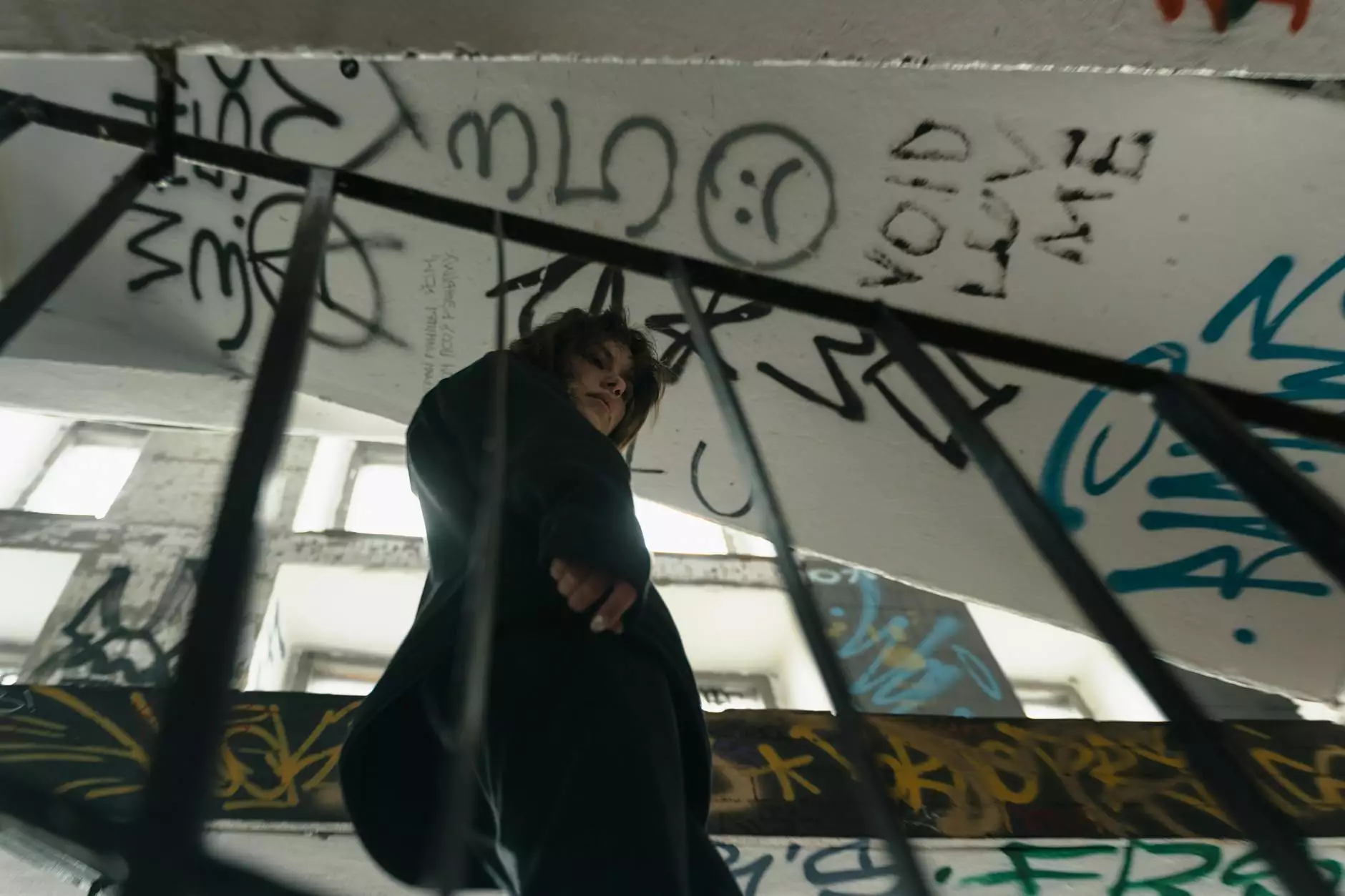
The world of manufacturing has evolved tremendously over the years, with plastic injection moulding taking center stage as one of the most effective and efficient methods to produce high-quality plastic parts. As a leader in this industry, Hanking Mould has established itself as a premier plastic injection mould manufacturer, delivering superior products that meet the diverse needs of our clients. In this comprehensive article, we will delve into various aspects of plastic injection moulding, its processes, benefits, and what sets us apart in the industry.
What is Plastic Injection Moulding?
Plastic injection moulding is a manufacturing process that involves injecting molten plastic material into a pre-designed mould to create specific shapes and forms. This technique is widely used across various industries due to its ability to produce parts in bulk, maintain a high level of precision, and reduce waste.
The Plastic Injection Moulding Process: A Step-by-Step Breakdown
The process of plastic injection moulding is intricate yet efficient. Here’s a detailed look at how it works:
- Material Selection: The process begins with selecting the appropriate type of plastic resin, which can be thermoplastic or thermosetting.
- Heating: The chosen plastic is then fed into a heating barrel where it is melted into a molten state.
- Injection: Once molten, the plastic is injected into a mould cavity under high pressure, ensuring that every detail of the design is captured.
- Cooling: The injected plastic is allowed to cool and solidify within the mould.
- Demoulding: Finally, the cooled part is removed from the mould, completing the manufacturing cycle.
Key Benefits of Using Plastic Injection Moulding
Opting for plastic injection moulding provides several advantages that make it a preferred choice for manufacturers across industries:
- High Efficiency: The speed at which parts can be produced is a significant advantage, allowing for mass production with minimal downtime.
- Precision and Accuracy: Injection moulding is renowned for its ability to produce finely detailed and accurate parts consistently.
- Material Versatility: A wide variety of plastic materials can be used in the injection moulding process, allowing for customization based on specific needs.
- Reduced Waste: The process minimizes waste material, as excess plastic can often be recycled and reused in future runs.
- Cost-Effective: While the initial setup may require investment, the overall cost per unit decreases significantly as production volumes increase.
Why Choose Hanking Mould as Your Plastic Injection Mould Manufacturer?
At Hanking Mould, we take pride in our reputation as a leading plastic injection mould manufacturer. Here are a few reasons why choosing us is the right decision for your business:
Expertise and Experience
With years of experience in the industry, our team possesses the technical know-how and expertise required to manage complex mould designs and production processes. We have a proven track record of delivering projects that meet the highest standards of quality and efficiency.
State-of-the-Art Technology
We invest heavily in modern technology and advanced manufacturing techniques, ensuring that our processes are not only efficient but also produce superior quality moulds. Our cutting-edge machinery allows us to push the boundaries of what is possible in the realm of plastic injection moulding.
Customized Solutions
Every client has unique needs. We pride ourselves on our ability to provide tailored solutions that address specific requirements. From design to production, our team collaborates closely with clients to ensure that we meet their exact specifications.
Quality Assurance
Quality is at the heart of what we do. We implement stringent quality control measures throughout the production process to ensure that every part we produce meets or exceeds industry standards. Our comprehensive testing protocols verify that our moulds perform well under various conditions.
Applications of Plastic Injection Moulding
Plastic injection moulding is utilized across a multitude of industries. Some of the most prominent applications include:
- Automotive Industry: Producing parts like dashboards, bumpers, and interior components.
- Consumer Goods: Manufacturing a wide range of products from toys to household items.
- Medical Devices: Crafting components for devices requiring high precision and reliability.
- Electronics: Providing housings and components for various electronic devices.
Eco-Friendly Practices in Plastic Injection Moulding
As environmental concerns grow, Hanking Mould remains committed to adopting eco-friendly practices in our operations. Here are some initiatives we implement:
- Material Recycling: We strive to use recycled plastics wherever possible to minimize our environmental footprint.
- Energy Efficiency: Our advanced machinery is designed to consume less energy without compromising performance.
- Waste Minimization: We actively seek ways to reduce waste during the manufacturing process.
Investing in Plastic Injection Mould Manufacturing: Tips for Businesses
If you are considering investing in plastic injection mould manufacturing, here are some essential tips to help you navigate the process successfully:
Conduct Thorough Research
Understand your industry requirements, the specific applications of the parts you need, and the types of materials available before making any decisions.
Select the Right Manufacturer
Choose a manufacturer with a strong reputation, proven experience, and the capacity to meet your production needs.
Focus on Design
Invest in proper design and prototyping stages. The design will significantly impact the efficiency and effectiveness of the moulding process.
Consider Long-Term Costs
While upfront costs are crucial, consider the long-term affordability of production and whether the manufacturer offers scalability for future growth.
Future Trends in Plastic Injection Mould Manufacturing
The plastic injection moulding industry is continuously evolving. Some expected trends that could shape its future include:
- Increased Automation: Automation technologies are likely to streamline production processes and enhance efficiency.
- Smart Manufacturing: The integration of IoT and data analytics will allow for real-time monitoring and optimization of production.
- 3D Printing: Although not a replacement, hybrid manufacturing approaches using 3D printing alongside traditional moulding could offer flexibility and reduce lead times.
Conclusion
In conclusion, plastic injection moulding stands as a pivotal component of modern manufacturing, providing businesses with the ability to produce high-quality parts efficiently and sustainably. At Hanking Mould, our commitment to innovation, quality, and customer satisfaction positions us at the forefront of the industry. Whether you are in need of a reliable plastic injection mould manufacturer or seeking expert insights into the moulding process, we are here to assist you every step of the way.
Embrace the future of manufacturing with Hanking Mould—where innovation meets excellence in plastic injection mould production.