Mold Tooling: The Backbone of Precision Manufacturing
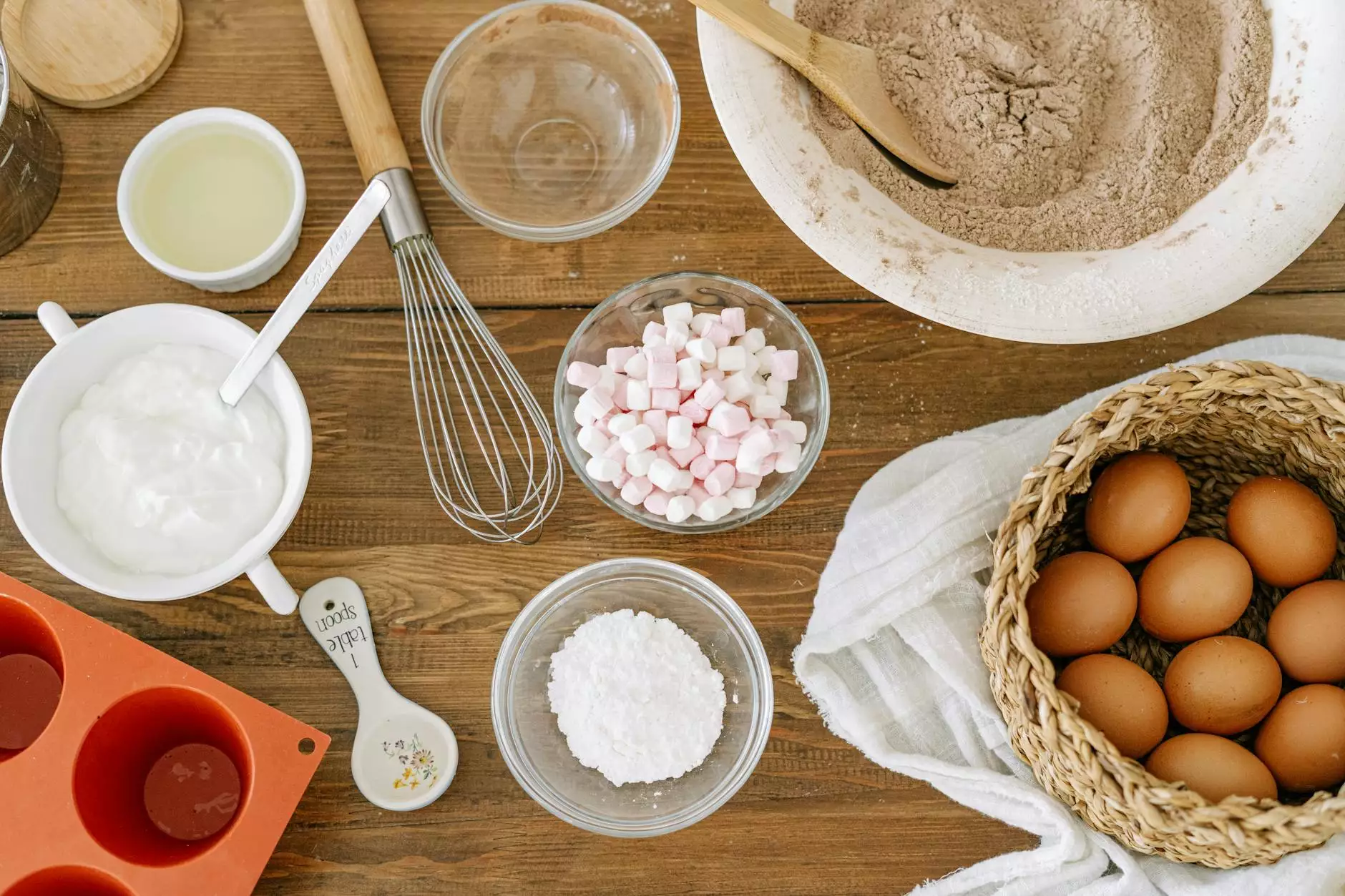
In the world of manufacturing, few components are as crucial as mold tooling. This process not only ensures the quality and efficiency of produced parts but also significantly influences the overall success of production lines. As businesses strive to stay competitive in the ever-evolving landscape of industrial production, understanding the intricacies of mold tooling becomes imperative.
What is Mold Tooling?
Mold tooling refers to the methods and processes used to create molds, which are then employed to shape materials into desired forms. This can involve a variety of materials, including metals, plastics, and composites. It is a critical aspect of manufacturing, particularly in sectors such as automotive, aerospace, and consumer goods.
The Importance of Mold Tooling in Manufacturing
The role of mold tooling extends beyond merely shaping materials. Here are several reasons why it is so vital:
- Precision: Mold tooling allows for the production of parts that meet stringent specifications and tolerances.
- Efficiency: Well-designed molds can significantly reduce production times and costs.
- Consistency: Mold tooling ensures that every part produced is uniform, which is essential for product quality.
- Innovation: Advanced tooling techniques enable the creation of complex geometries that push the boundaries of design.
The Mold Tooling Process Explained
Understanding the mold tooling process is essential for manufacturers looking to optimize their output. The process typically involves the following steps:
1. Design of the Mold
The initial step involves the detailed design of the mold. This stage requires a deep understanding of the part to be produced as well as the materials that will be used. CAD (Computer-Aided Design) software is typically utilized to create a precise mold design that reflects all necessary specifications.
2. Material Selection
Choosing the right materials for mold tooling is critical. Common materials include:
- Steel: Highly durable and able to withstand high temperatures, making it suitable for long production runs.
- Aluminum: Lightweight and quicker to manufacture, ideal for lower-volume production.
- Composite materials: Used for specialized applications where unique properties are needed.
3. Machining the Mold
Once the design is finalized and the materials selected, the next stage is machining. This involves using various machining techniques to fabricate the mold. This could include:
- Milling: Removing material from the mold to create the desired shapes.
- EDM (Electrical Discharge Machining): A method used to produce intricate shapes that are difficult to achieve through traditional machining.
- Laser cutting: Offering ultimate precision for complex designs.
4. Assembly and Testing
After machining, the components of the mold are assembled. This phase may involve multiple parts that need to fit together perfectly. Following assembly, testing is crucial to ensure that the mold performs correctly and produces high-quality parts.
Key Benefits of Effective Mold Tooling
Effective mold tooling brings several advantages, which can have a profound impact on productivity and profitability:
- Cost Reduction: By minimizing material waste and reducing production time, businesses can significantly lower costs.
- Enhanced Product Quality: Consistent and precision in the molding process ensures that the products meet customer expectations.
- Faster Time-to-Market: A streamlined mold tooling process enables manufacturers to bring new products to market more quickly.
- Improved Flexibility: Advanced mold tooling techniques allow manufacturers to quickly shift from one product to another without extensive downtime.
Challenges in Mold Tooling
While mold tooling has numerous advantages, there are also challenges that manufacturers must navigate:
- High Initial Costs: The initial investment for quality tooling can be substantial.
- Maintenance and Repairs: Regular maintenance is required to ensure that molds remain in optimal condition.
- Design Limitations: Certain complex geometries can be difficult to achieve, requiring innovative solutions.
Best Practices for Optimizing Mold Tooling
To maximize the benefits of mold tooling, manufacturers should adopt various best practices:
1. Invest in Training and Skills Development
Ensuring that engineers and machinists are well-trained in the latest mold tooling technologies and methods is essential. Continuous education helps to keep skills sharp and encourages innovative thinking.
2. Embrace Advanced Technologies
Utilizing advanced manufacturing technologies, such as 3D printing for prototyping and CNC machining for production, can enhance efficiency and accuracy in mold tooling.
3. Optimize Design for Manufacturability (DFM)
Considering manufacturability during the design phase can significantly streamline the tooling process. This involves evaluating how easily a part can be manufactured and identifying design tweaks that could simplify the mold.
4. Implement a Robust Maintenance Schedule
Regular maintenance of molds not only extends their lifespan but also ensures consistent output quality. Detailed records of maintenance activities can help identify issues before they impact production.
The Future of Mold Tooling
The evolution of technology continues to reshape the landscape of mold tooling. Trends to watch for include:
1. Automation and Robotics
The incorporation of automated processes and robotics is set to increase precision and decrease lead times in mold making and part production.
2. Sustainability Initiatives
As pressure for sustainable practices rises, mold tool manufacturers are exploring eco-friendly materials and processes. This may include using biodegradable plastics and reducing energy consumption.
3. Integration of IoT (Internet of Things)
The integration of IoT technology into mold tooling processes allows manufacturers to collect data in real-time, enabling better decision-making and predictive maintenance.
Conclusion
In conclusion, mold tooling stands as a cornerstone of modern manufacturing, directly influencing efficiency, product quality, and overall business success. As industries continue to evolve, embracing advancements in technology and best practices will allow businesses to stay competitive and meet the ever-changing demands of the market. By investing in mold tooling strategies, companies can not only enhance their production capabilities but also lay the groundwork for sustainable growth.